Ai Indigo 藍染
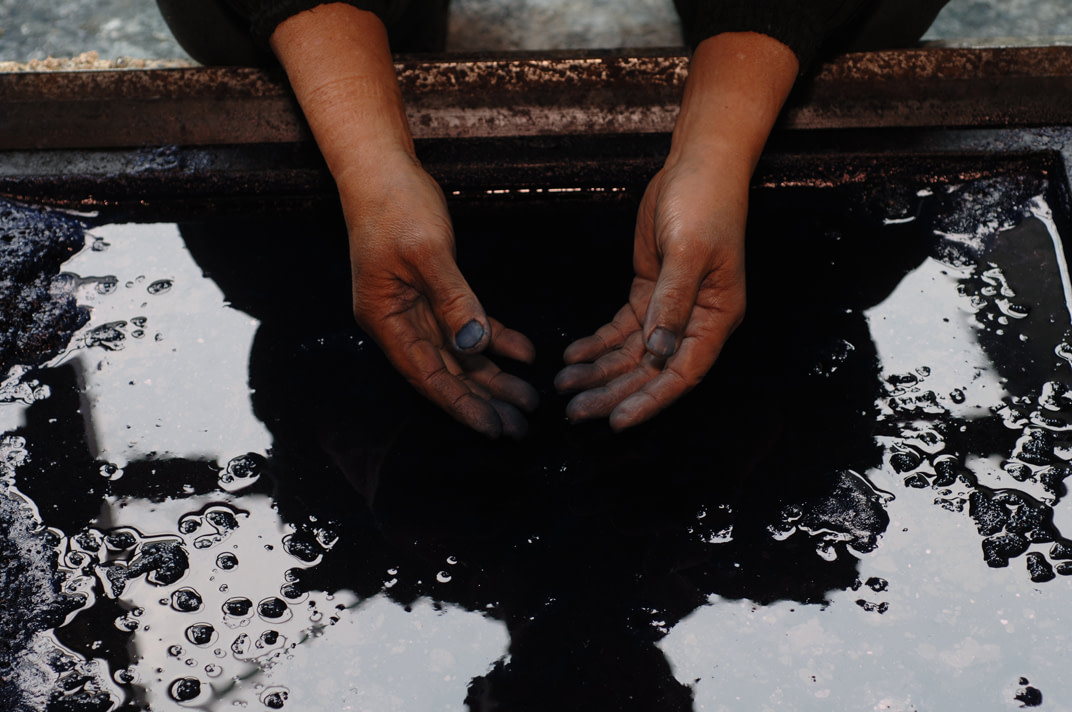
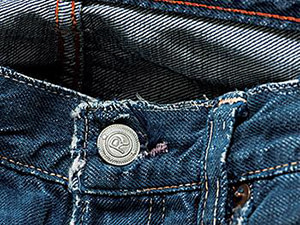
At 45R, we are known for the variety of garments we offer in indigo or Ai-dye. All of our indigo-dyed garments are yarn dyed, not garment dyed, in order to achieve a rich dark blue color. Indigo-dyed items fade beautifully over time, and our denim products dyed with indigo age especially well with a high contrast between the blue dye and the white of the yarn.
When we refer to Ai-dyed items, we are talking about a Japanese natural plant dye. This is 45R’s signature color – Ai-indigo. We are fascinated by Ai-indigo for its ability to create millions of expressions. Garments which are Ai-dyed at 45R are always yarn-dyed by hand. For example, with Ai-dyed denim, the skins of yarn are dyed twice a day for two weeks using 100% all natural Ai-indigo to achieve their fullest color.
In the beginning
Ai dye can’t be produced without going through the hands of masters in various fields. Different from a chemical dye, Ai-dye (Japanese indigo) starts from growing Ai plants. Because they are natural plants, there may be a good year and a bad year in terms of production. After being harvested from the fields, Ai plants are fermented for 100 days. It takes about a year to produce an item dyed with Ai.
Ai is a living thing. Those who work with Ai can’t be away from it for a long time. A long vacation? There is no chance. Ai-dye is a product of those masters who have earned skills and experience by spending nights and days for their mastery.
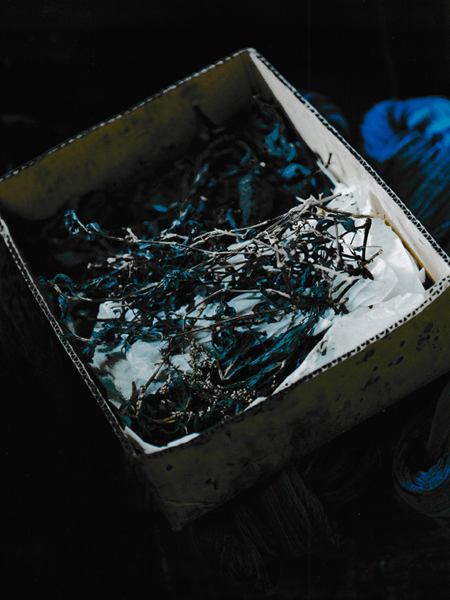
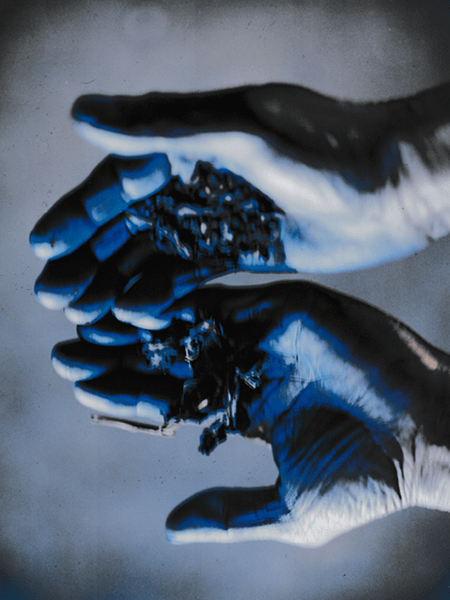
Ai Master
Toyama family, Tokushima, Japan.
Mr. Toyama’s family has been producing Ai for the past five generations and is now one of a few Ai producers still exists in Japan. Mr. Toyama has been awarded for his mastery from the government of Japan. Fermented Ai is called Sukumo. Sukumo can be produced only for about 50,000 lbs a year. 500 lbs of Sukumo costs more than a couple of thousand of dollars.
Ai-Dye Masters
Asai family, Kyoto, Japan
Mr. Masafumi Asai and his son Naoyuki have been working with 45R for Ai-dye items. Mr. Asai Sr. started his career as a batik artist for Japanese traditional “kimono”. He dyes with his bare hands. His hands and nails are permanently dyed with deep indigo blue.
Ai Kame (Pots)
These pots buried underground can contain about 300-500 litter of Ai-dye in liquid form.
This Ai-dye liquid is the mixture of Sukumo (fermented indigo), ash water (the supernatant of the mixture of hot water and ash), Japanese sake, Fusuma (flour bran) and alkali water.
After about 2 weeks, the fermentation process starts to show on the surface of the liquid in the form of bubbles. These bubbles are called “flower of Ai”.
Once you dip an item into this Ai-dye, Japanese sake is added to the mixture in the pot to revitalize the Ai dye.
Sukumo can be used for about 3 months by repeating this revitalization process – drinking “Sake”.
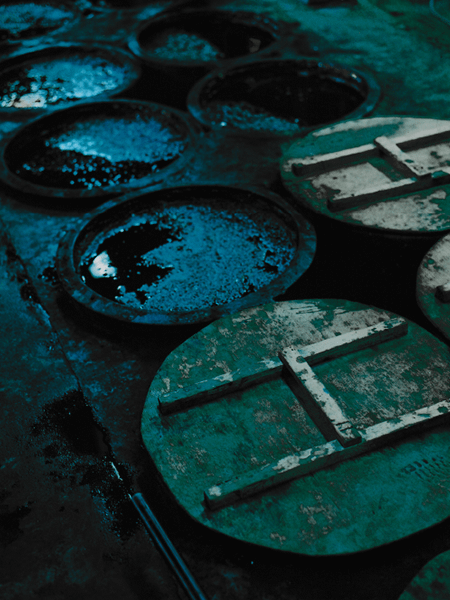
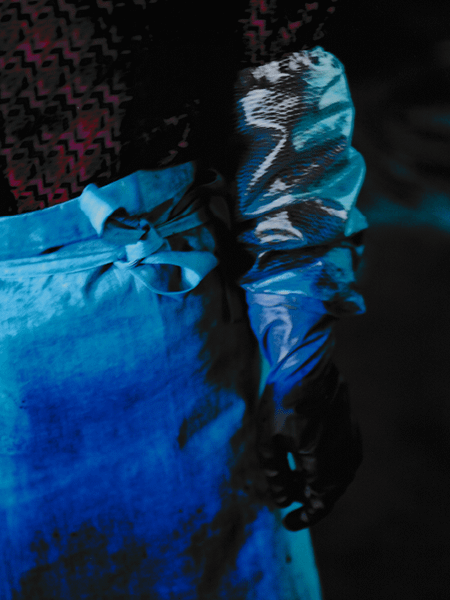
Indigo Blue – Japan Blue
When Commodore Perry first arrived in Japan in 1853 to demand the Tokugawa shogun the opening of Japan ports, he was very surprised by how often he saw indigo items including clothing and housewares among the people of Japan.
Ai has been very close to Japanese living for a long time.
Patience with Ai
The process of Ai-dying is time consuming.
Dip yarn in the indigo pot. Dry it in the air to oxidize. The oxidation dyes yarn deeper in indigo. Rinse with well water after oxidation to remove the scum from Sukumo. Repeat the same process again and again…
The photo shows how the raw yarn gets deeper in indigo each time you repeat the dying process. 45R’s Aihiko is dipped in indigo twice a day for fourteen days. Once they become yours, Aihiko starts the fading process by your hands.
Ito Guruma – Spinning Wheel
Yarn is dyed in bundles.
After yarn is dyed in Ai indigo, it is wound on a spinning wheel. Then, the end of yarn is wound on a warp beam in preparation for weaving.
Shuttle Loom Machine – Old Style
We use traditional shuttle loom machines.
The shuttle runs horizontally between warps making loud noise. It’s almost like a grumpy grandfather making sure that we are aware that he is working hard.
This old machine is the one that can produce slubby, uneven texture of good durable denim, like your grandfather’s old denim.
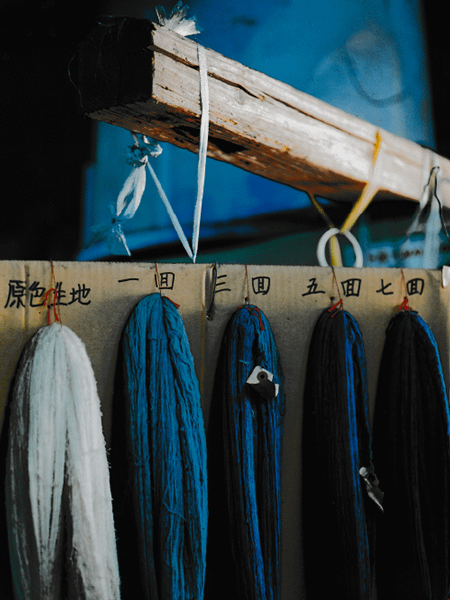
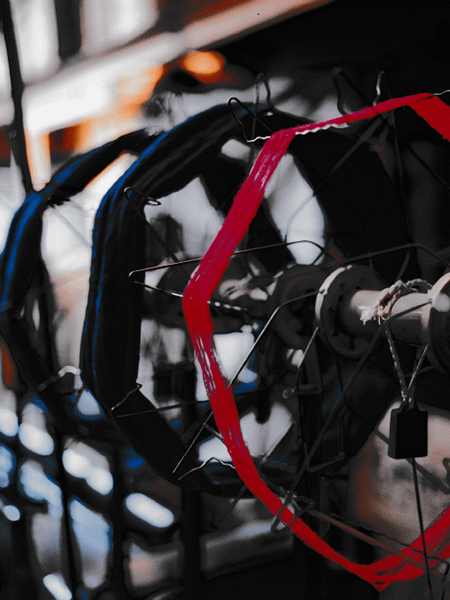
From one hand to another
Once yarn is dyed, it is sent to our weaving shop where it becomes a sheet of fabric.
Then, the fabric is delivered to our sewing factory where the fabric is cut into different parts and sewed together to make a piece of clothing.
Then, these pieces are sent to our finishing shop for final touch such as distressing or washing denim.
Pattern-makers – Modelists
The patternmakers at 45R are not only to draft patterns and make samples based on the designer’s sketches, but also to manage the production costs.
Our pattern-makers are called “modelists” and the department they work for is called “modelist department”.
Rivets – Carving the History of Brand
45R’s current rivet is our second rivet design. It first came out in the year 2000 when we first opened the SoHo, New York store and the head store, Badou-R, in Tokyo to celebrate the brand-new start of 45R brand, which is a new development from our original brand concept focusing denim products.
45R – What We Do
We, 45R, produce durable and timeless pieces that involve hand work in the process of making, using traditional techniques that have been passed on, reflecting “what’s in” and seasonal motifs in the designs.
We wish to deliver happiness and excitement with our works.
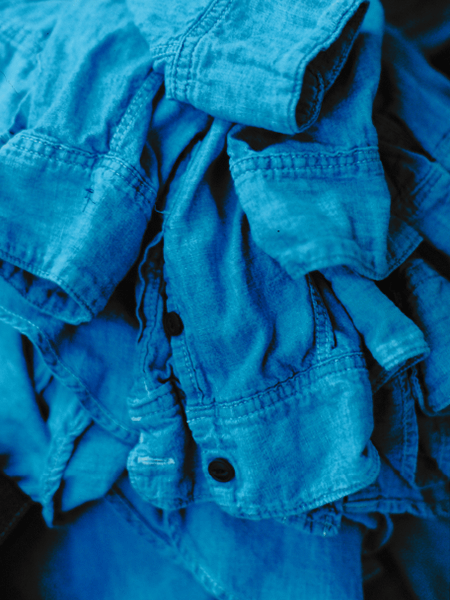
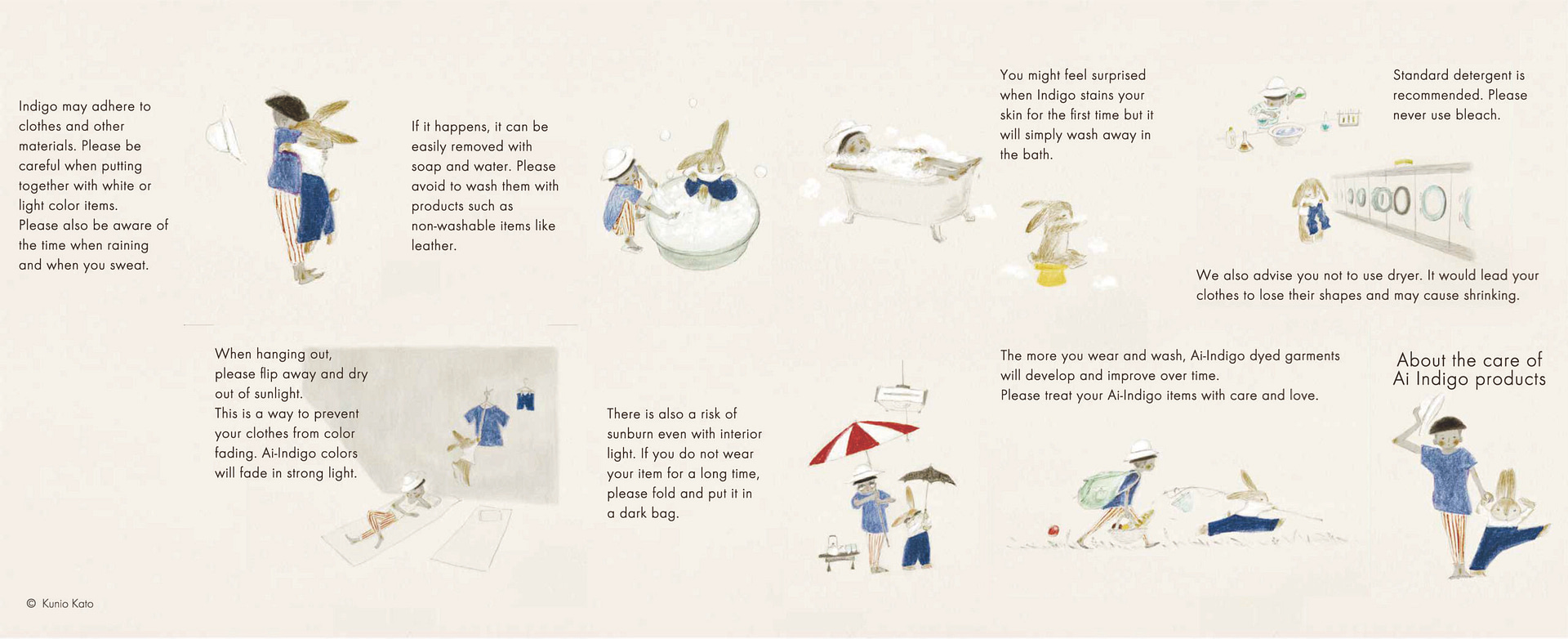